Tampa, Florida
Meeting Design & Facilitation By
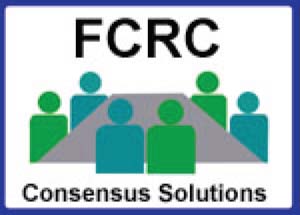
Report By Jeff A. Blair Florida Conflict Resolution Consortium Florida State University
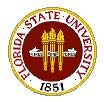
jblair@fsu.edu http:// consensus.fsu.edu
This document is available in alternate formats upon request to Dept. of Community Affairs, Codes & Standards, 2555 Shumard Oak Blvd., Tallahassee, FL 32399, (850) 487-1824.
GARAGE DOOR AND SHUTTER LABELING WORKGROUP REPORT
SEPTEMBER 14, 2006
Overview
Raul L. Rodriguez, AIA, Chair of the Florida Building Commission, has made appointments to the Garage Door and Shutter Labeling Workgroup, and they are found below. At the July 2006 Commission meeting, based on the Window Workgroup’s recommendations, the Commission created a Garage Door and Shutter Labeling Workgroup, charged with developing recommendations regarding the labeling of garage doors and shutters. As with the Window Labeling Workgroup, the focus for the Garage Door and Shutter Labeling Workgroup will be to provide building officials, in a field useable format, with the information they need to ensure that garage doors and shutters comply with the Florida Building Code.
Workgroup Membership
The following members were appointed to serve on the Window Workgroup:
Joe Belcher, Bob Boyer, Jack Glenn, Herminio Gonzalez, Darius Grimes, Jeffery Gross,
Joe Hetzel, Do Kim, C.W. Macomber, Frank O’Neil, Mike Salmon, Sigi Valentine, and
Dwight Wilkes.
MEETING REPORT
Opening and Meeting Attendance
The meeting started at 9:30 AM, and the following Workgroup members were present: Herminio Gonzalez, Darius Grimes, Do Kim, C.W. Macomber, Frank O’Neil, Mike Salmon, and Dwight Wilkes. (Scott Hamilton sat in for Joe Hetzel)
DCA Staff Present
Rick Dixon, Mo Madani, and Betty Stevens.
Meeting Facilitation
The meeting was facilitated by Jeff Blair from the Florida Conflict Resolution Consortium at Florida State University. Information at: http://consensus.fsu.edu/
Project Webpage
Information on the project, including agenda packets, meeting reports, and related documents may be found in downloadable formats at the project webpage below:
http://consensus.fsu.edu/FBC/gdslwg.html
Meeting Objectives
The Workgroup voted unanimously, 7 -0 in favor, to approve the agenda as presented including the following objectives:
- To Review Work Group Procedures and Guidelines
- To Hear an Overview of Workgroup’s Charge and Scope
- To Identify Inspection and Enforcement Issues to Ensure Garage Doors and Shutters Comply with Wind Pressure Requirements
- To Propose Options for Evaluation
- To Evaluate, Rank, and Refine Proposed Options
- To Consider Public Comment
- To Identify Needed Next Steps: Information, Assignments, and Agenda Items for Next Meeting
Work Group’s Decision-Making Procedures and Meeting Guidelines
Jeff Blair reviewed the Workgroup’s decision-making procedures found on page 4 of the agenda packet.
Overview of Workgroup’s Scope and Charge
Jeff Blair explained that the scope and purpose of the Workgroup is to provide recommendations on how to provide building officials with needed information for conducting field inspections to ensure garage doors and shutters comply with the Florida Building Code.
Review of Window Labeling Workgroup’s Recommendations
Jeff Blair reviewed the Window Labeling Workgroup’s recommendations with the Garage Door and Shutter Labeling Workgroup in order to provide examples of issue and options relevant to labeling. The Window Labeling Workgroup’s recommendations may be found at the following webpage: http://consensus.fsu.edu/FBC/wwg.html
Identification of Inspection and Enforcement Issues to Ensure Garage Doors and Shutters Comply with Wind Pressure Requirements
Workgroup members and members of the public were invited to offer a list of issues they believe should be evaluated by the Workgroup. A separate discussion was conducted for garage doors and shutters. The results of the discussions are found beginning on page 3 of this report.
Next Steps
- Next meeting will be November 13 – 14, 2006 in Tampa.
- Members should consult with their constituency and provide specific options to address each of the key issues identified by members and the public during the September meeting.
- The Workgroup will evaluate and rank each of the options and adopt a package of consensus recommendations for submittal to the Commission.
Adjournment
The Workgroup voted unanimously, 7 – 0 in favor, to adjourn at 11:06 AM.
ISSUES IDENTIFICATION EXERCISE RESULTS
During the meeting, Workgroup members were asked to identify the key issues that should be considered, as well as identify a preliminary list of options.
At the November meeting members will be asked to consider the range of issues identified by the Workgroup’s building officials and to propose options to address the issues. For each issues in turn, the Workgroup will be asked to propose the full range of options, to propose additional options, to seek clarification on the intent of each option, and then to evaluate each option using a four-point acceptability scale, where a 4 is acceptable, a 3 is minor reservations, a 2 is major reservations, and 1 is not acceptable.
Following the initial and additional evaluations, Workgroup members will be requested to explain their range of concerns, and to identify any additional information they need in order to further consider the issue and/or option. The Facilitator explained that in general a 4 or 3 represents support for the option, and a 2 or 1 represents a lack of support for the option.
The following scale will be utilized for the ranking exercises:

GARAGE DOOR ISSUES
Issues Identified by the Workgroup’s Building Official Members
Need to link paper work to the product being installed: including the model number, series, etc. Need identification mark, on a permanent or temporary label, perhaps a metal stamp, FL#, Miami-Dade NOA#, DP positive and negative rating of the product (meet minimum DP rating), On multiple series list: make and model, anchoring, installation instructions of product.
Maybe use thee back of the label. Details are already part of product approval, labeling requirements for windows should be in the Code, performance, manufacturer, testing agency, manufacturer, impact resistant product, start with the code labeling requirement, code change submitted requiring labeling, create a prescriptive section of the code requiring labeling like windows.
Need a permanent label on the product with product information and a temporary, supplemental label for instructions, too sophisticated for one label. Need permanent label with key information and supplemental label for greater detail, including installation instructions.
Need to label for pressures and not wind speeds.
Discussion, Issues, and Options—Garage Doors
- 16 ft. garage door sections can be made to withstand different wind speeds. Could be installed for 110 or 120 depending on the structural supports behind it, track, door rating, match fastener spacing. The label could be filled in at time of installation specifying what was installed. Fill in check box matching installation procedures followed.
- 120/130 mph or psf? Based on location of structure, need to request that it be expressed in PSF. 25-40 psf, match installation instructions.
- There are 250 different doors, basic door, 10 different door blanks, 15-20. There are option codes, basic panel on door, wind speed rating, approvals have option codes listed, label require option code, would produce many different labels, manufacturer could not put label on door, someone needs to apply the label.
- Manufacture does not have control over installation, label would be applied at installation.
- If product is delivered in the field and label is missing, how would this address labeling? Certification agencies have specific labels and verify products in the field.
- Not all certification programs do their labels the same way, not consistent in application of labels.
- Every garage door has an installation drawing that covers that installation for that rating, reinforcement requirements, jamb requirements, they will be at job site with the door. Match installation to the drawing.
- If additional hardware is required to be installed to bring it to a certain strength, should show this on the label, preferably the permanent label.
- There should be traceability to the manufacturer for the permanent label, if use preassembled components, actuators, should be traceable through the dealers.
- Garage doors field assembled, installers buying components from different companies or use what was tested. Need to hold installer accountable through traceability.
- If they come as a kit, with the track, can the installer change the installation components from the package.
- Dealers are buying parts from different companies.
- Product Approval system approval should be on the door, component substitution by dealers needs to be addressed.
- The Code allows substitute components as long as they are approved, label would have to address this in some manner.
- Labels are for standard products.
- Each specific case is subject to local approval.
- With component substitutions, do not know if will perform to the same as approved assemblies.
- With large buildings with engineers of record, substitution is fine.
- For single family applications they do not have an engineer of record, store sends out installer to the homeowner, does the homeowner need to hire an engineer to install the door?
- The kits may not provide fasteners.
- Labeling could disallow substitutions.
- A 3/8” bolt is a 3/8” bolt, can go beyond but not less than specified, for substitutions.
- Rail thickness, are the back up angle irons that reinforces doors tested? Does the manufacturers representative certify that it was installed correctly?
- The company does not extend approval to assembly of outside components.
- Need to clarify in the Code whether outside/substitution components can be used.
- Components have part numbers, stamp showing yield strength in the drawings, put on labels, too much information for a label.
- Temporary label could be clear plastic seal, rip off and use.
- Building official can always require information to be on the job site at time of inspection, would be nice if there was language in the code requiring this.
SHUTTERS
Issues Identified by the Workgroup’s Building Official Members
Need a prescriptive attachment method, that will work for all scenarios, similar to doors,
permanent or temporary, peel off, or stamped on product.
Require the same information as for windows: the manufacturer, DP rating.
Should ban wind speeds on windows, instead use psf. They are designed for wind pressures not
wind speeds.
Discussion, Issues, and Options—Shutters
- The minimum information needed should be on the label, supplement labels, installation instructions, duplicative, plans reviewer has information, traceability on label, should lead you to find where the information is located.
- Should be permanent with the information on the label: where did the product come from, who was the manufacturer, stamped, pasted decals (licensing tag).
- There are different types of shutters, fabric, roll, label for all manufacturers.
- With panels, should every panel have label? Or just the system?
- There are different practices in different areas of the State. Need installation instructions for homeowners, no requirement in the western part of the State, need consistent requirements in the State.
- We do have some problems with shutters, prescriptive, 2 or 3 types of bucks, installations, retrofit market, minimum design pressure. Should simply refer to installation instructions, 40 different fasteners to achieve different design pressures, support having design drawings on the job site to ensure correct installation for the site specific conditions.
- Need a set of prescriptive defaults for installation instructions with overwriting, DASMA has a technical data sheet with different design pressures. This could be condensed. If limited to fastening to wood jambs, limit number of door sizes, could condense instructions.
- Engineers make detailed designs and instructions, for worst case scenario(s).
- Labeling, prescriptive attachment schedule, cuts out product approval for those products, what passes, should put prescriptive methods of attachment in the Code.
- Could do the same thing with foundations, what does the building official want, plan review process, field inspector needs to know what to look at, does he need to look on a computer or can he look at something on the site?
- 2 inches o.c.: need prescriptive code section, or use engineering. Need design pressure and spacing, garage doors go to clean buck, shutters do not have a clean frame, they have different materials to conform to, must specify screw and substrate.
- Should require engineering on site at the time of inspection.
- Improved installation drawings are not on the job site.
- Require documents at the job site.
- DP on shutters, manufacturer will not know what the DP is for the shutter, attachment spacing affects DP of shutter.
- Shutters are not put up at time of inspection, how can they be inspected if not installed?
- Shutters are not listed in list of required inspections.
- Make it mandatory that drawings be on job site, for permitting, require the dealer to submit drawings, not just model number. The plans examiner should confirm that what is on the job site is the what is on the plans.
- Worst case anchor and anchor spacing for inspector to check.
- DASMA is developing a certifying program for shutters.
- Shutter systems allowed to destroy what is inside? That is a Code issue.
- Do not have to hold to criteria of a label, reinforcement/
- Inspection or non inspection of shutter units, around sliding glass doors. It is a manufactured product, anchors are not sufficient, can not tell what is done.
- Glass breakage is allowed.
- Labeling identifies whether tested as a porous product or non-porous product allowing deflection.
- Association systems, high tech. 100 have approval set up fabricators who install in the field, loose labeling system in the process, not using labeling system, labeling not required, add labeling requirement to the code for fabricator/installer (traceable to fabricator/installer) who certifies the label QA process, inspections, model number tells manufacturer. Need traceability.
- West coast requires picture of installation.
- Should require one panel to be mounted. In Palm Beach builders are providing video packages showing how to install panels, with s diagram, panels are numbered by windows for the homeowner.
- For existing buildings: need to require same standards as for new construction. This needed to be addressed.
- Some jurisdictions are not requiring building permits for putting up shutters.
Testing of Shutters should be implemented: In lieu of the fact that there is no published test standards shutters should be tested in accordance with ASTM E 330 Procedure A at a load of 1.5 times the required positive and negative design pressure load. The load shall be sustained for 10 seconds with no permanent damage to fasteners, hardware parts, or any other damage, which causes the shutter element to be nonfunctional. Products for the HVHZ shall comply with TAS 202. The maximum deflection shutter elements under positive and negative load should be recorded. The deflection data will determine the shutters safe mounting distance away from the fenestration product in the opening. Shutters used in the windborne debris regions, upon successful testing to ASTM E 330, should be impact and cycle tested in accordance to ASTM E 1886/1996. Sheeting type of shutters may be penetrating the building envelop (windows and doors) when impacted by windborne debris. The work group should carefully review whether or not this constitutes a product failure; falls under partially enclosed requirements or is acceptable in view of “Life Safety” issues.